АБС-пластик
АБС-пластик -термопластичная пластическая масса на основе акрилонитрилбутадиенстирольного привитого сополимера, имеющая двухфазную структуру. Непрерывную фазу (жесткую матрицу) составляет сополимер стирола с акрилонитрилом, дискретной фазой служит дивинильный, бутадиен-стирольный или бутадиен-нитрильный каучук с размером частиц 0,5-2 мкм. Каучуковые частицы окружены тонким слоем привитого сополимера строения (один из наиболее вероятных вариантов):

В структуре макромолекулы привитого сополимера главная цепь представляет собой гомополибутадиен либо двойной сополимер бутадиена со стиролом (бутадиенстирольный синтетический каучук) или акрилонитрилом (нитрильный синтетический каучук), а боковые прививки - сополимеры стирола и акрилонитрила. Таким образом, привитой сополимер имеет достаточноe сродство как к матрице, так и к дискретной фазе, служит межфазным переходным мостиком и обеспечивает хорошую адгезионную прочность композиции. Каучуковая частица, имеющая хорошую адгезию к матрице благодаря привитому сополимеру на ее поверхности, деформируется при приложении нагрузки без изменения объема. Общее содержание мономерных звеньев в сополимере лежит в пределах: стирол - 25-80%, бутадиен - 10-40%, акрилонитрил - 5-35%. В состав отдельных марок АБС-пластика могут входить звенья - остатки α-метилстирола и метилметакрилата.
АБС-пластик может быть получен тремя методами:
1) привитой сополимеризацией сомономеров стирола и акрилонитрила на каучук, 2) сокоагуляцией латексов каучука и сополимера стирола с акрилонитрилом, 3) механохимическим (механическим смешением расплавов каучука и сополимера СН в присутствии пероксидов в смесителе типа Бенбери).
При сокоагуляции латексов получают механическую смесь каучука и сополимера, не содержащую привитого сополимера. Качество получаемого при этом пластика уступает другим способам.
Механохимический метод позволяет получать как блок-, так и привитые сополимеры. В присутствии пероксидных инициаторов (например, пероксида бензоила) получают в основном привитые сополимеры:
В отсутствие инициаторов образуются только блоксополимеры:
Привитая сополимеризация в сравнении с другими методами отличается рядом преимуществ: а) позволяет получать полимер с более равномерным составом, б) более высокие физико-механические показатели сополимера, в) лучшая перерабатываемость пластика в изделия. Эти преимущества обусловлены тем, что привитая сополимеризация позволяет достаточно тонко регулировать морфологическую структуру АБС-пластика, включающую широкий спектр дисперсных каучуковых частиц размером от долей мкм до 2 мкм. При этом упрочнение полимера протекает в равной степени по трем механизмам (крейзообразование, сдвиговая текучесть, взаимодействие крейзов и полос сдвига).
Химизм привитой сополимеризации в зависимости от способа проведения процесса включает одну или две стадии. Сначала периодической эмульсионной полимеризацией получают латекс синтетического каучука (гомополибутадиен, сополимер бутадиена со стиролом или акрилонитрилом) - дискретные частицы АБС-пластика:
или готовят раствор каучука в мономерах.
Затем в реакторе непрерывного действия в присутствии инициатора (предпочтительно пероксиды) проводят процесс привитой сополимеризации стирола и акрилонитрила на каучук (образование межфазного слоя):
На начальных этапах процесса прививка идет за счет отрыва атома водорода α-метиленовых групп, а на глубоких стадиях - также путем раскрытия кратных связей. Одновременно протекают процессы синтеза статистического линейного сополимера стирола с акрилонитрилом (образование матрицы):
Предпочтительность пероксидов в качестве инициаторов обусловлена пониженной энергией активации их распада на свободные радикалы. Пероксиды при 65 °С отрывают атом водорода от молекулы эластомера, способствуя повышению как степени, так и эффективности прививки (массовая доля каучука, макромолекулы которого содержат хотя бы одну привитую цепь), в то время как азосоединения (например, порофор N) образуют привитой сополимер при температуре выше 100 °С. На эффективность прививки оказывают влияние не только природа инициатора и температура процесса, но и строение главной цепи каучука. С увеличением содержания 1,2 звеньев эффективность прививки возрастает, так как при этом облегчается отрыв третичного атома водорода метиновой группы и интенсифицируется реакция сополимеризации между радикалами мономеров и боковой винильной группой:
Производство АБС-пластика чаще организуют в периодическом режиме, реже в непрерывном. Основным промышленным способом проведения привитой сополимеризации является эмульсионная полимеризация (периодический и непрерывный процессы). Блочный до неполной конверсии мономеров в непрерывном режиме и блочно-суспензионный способы полимеризации являются вторыми по значению. Особенностью механизма эмульсионной полимеризации как на стадии получения каучукового латекса, так и на стадии привитой сополимеризации является образование морфологических структур типа "ядро-оболочка". Установлено, что мономер внутри полимерно-мономерной частицы распределяется неравномерно, концентрируясь у поверхности, а полимер по причине снижения конфигурационной энтропии макромолекул у поверхности частицы стремится к центру частицы. В результате прививки образуются частицы АБС-пластика, состоящие из эластомерного ядра диаметром около 0,5 мкм, окруженного оболочкой сополимера толщиной 0,1 мкм. Небольшая часть сополимера образует инклюзии внутри эластомера.
Непрерывное производство АБС-пластика эмульсионной привитой сополимеризацией включает десять технологических стадий: I - подготовка сырья, II - получение латекса (полимеризация бутадиена или сополимеризация бутадиена со стиролом или акрилонитрилом), III - отделение непрореагировавшего бутадиена и других сомеров, IV - смешение латекса с сомономерами, V - привитая сополимеризация каучука с сомономерами, VI - отгонка непрореагировавших мономеров, VII - коагуляция латекса и выделение (осаждение) полимера, VIII - промывка полимера, IX - сушка и таблетирование порошка, X - грануляция и упаковка таблеток.
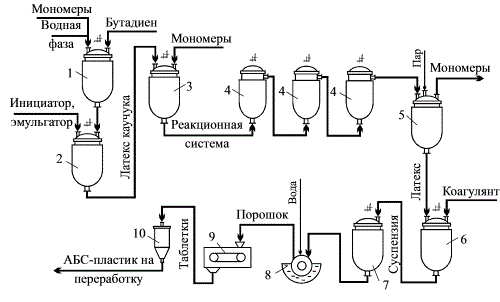
В реактор периодического действия 1 загружают водную фазу, содержащую эмульгатор (соли высших жирных кислот ряда С10-С16) и инициатор (персульфат калия), и при работающей мешалке бутадиен (при необходимости стирол или акрилонитрил, иногда для структурирования каучука вводят n-дивинилбензол) по рецептуре (в м.ч.): бутадиен - 100, вода - 200, эмульгатор – 2, инициатор - 0,5.
Подачей пара в рубашку создают температуру 60-80 °С. При этом за счет упругости паров мономеров (температура кипения бутадиена -4,47 °С) в реакторе создают избыточное давление 0,2-0,5 МПа и ведут процесс эмульсионной полимеризации в течение 5-6 ч до образования латекса (до степени конверсии 75%). Латекс каучука подвергают демономеризации (отгонке непрореагировавших бутадиена и сомономера), охлаждают до 40-50 °С и сливают в сборник-хранилище 2, где вводят дополнительное количество эмульгатора (соли жирных кислот ряда С10-С16) и инициатора (K2S2O8).
Смесь латекса с добавками дозировочным насосом непрерывно подают в смеситель 3 и смешивают с непрерывным потоком поступающих сюда сомономеров (стирола и акрилонитрила). Исходная реакционная система непрерывно поступает в первый корпус комбинированного реактора батарейного типа 4 объемом 20-30 м3. В батарее 4 при температуре 65-80 °С и атмосферном давлении протекает непрерывный процесс сополимеризации стирола и акрилонитрила и прививки цепей на каучук. Степень конверсии мономеров при среднем времени пребывания в реакторе 5-6 ч достигает 96-98%. Латекс привитого сополимера из последнего корпуса реактора 4 направляют в отгонный аппарат 5, где острым паром и под вакуумом при температуре 80 °С отгоняют непрореагировавшие мономеры. Конденсат отгонных паров возвращают в цикл. Демономеризованный латекс подают на стадию коагуляции в аппарат 6, где при температуре 40-65 °С действием алюмокалиевых квасцов (AlK(SO4)2) латекс разрушают. Образующаяся при этом суспензия порошкообразного полимера через сборник 7 поступает в барабанный вакуум-фильтр непрерывного действия 8, где порошок полимера подвергается промывке и отжиму до влажности 50-60%.
В ленточной сушилке 9 при температуре 80 °С полимер сушат потоком горячего воздуха до конечной влажности 1% и таблетируют валковым приспособлением. Из бункера 10 таблетки пластика направляют на смешение с красителем, другими добавками и грануляцию.
Производство АБС-пластика способом эмульсионной привитой сополимеризации характеризуется тремя основными недостатками: 1) необходимостью дорогостоящей водоподготовки и, следовательно, очистки большого количества токсичных сточных вод, 2) трудностью сушки тонкодисперсного порошка полимера и необходимостью грануляции его перед переработкой в изделия, 3) низкие диэлектрические показатели полимера (из-за присутствия электролита в процессе синтеза в эмульсии).
Блочный способ производства АБС-пластика в сравнении с эмульсионным способом при несколько пониженных качественных показателях имеет ряд преимуществ: 1) снижение капиталовложений в 2,5 раза и себестоимости продукции на 20%, 2) уменьшение энергоемкости в 2 раза, 3) повышение производительности труда в 5 раз. Технология блочного способа аналогична технологии гомополистирола блочным способом до неполной конверсии мономера с той лишь разницей, что в первый корпус комбинированного реактора батарейного типа, кроме стирола, подают акрилонитрил и раствор каучука в стироле. Блочную привитую сополимеризацию при ступенчатом повышении температуры проводят как в присутствии инициатора, так и без него.
Разделение фаз происходит в результате взаимной несовместимости каучуковых дискретных частиц с сополимерной матрицей. Привитой сополимер, главная цепь которого химически родственна дискретной фазе, а боковые цепи - матрице, дислоцируется на границе раздела фаз, выполняя функции эмульгатора системы. Взаимная несовместимость каучука и непривитого сополимера матрицы обусловлены разностью их параметров растворимости [?каучук = 17,2 (МДж/м3)1/2, а ?сополимерСН = 19,65 (МДж/м3)1/2] Параметр растворимости - характеристика вклада каждой молекулы жидкости в энергию взаимодействия:

где ПЭК - плотность энергии когезии, Дж/м3 ,
ΔUиспарения - энергия испарения единицы объема жидкости, Дж,
vж - мольный объем жидкости, м3 .
Параметр растворимости полимеров непосредственно измерен быть не может, его оценивают по равновесной степени набухания трехмерного (сшитого) полимера в ряду растворителей: параметр растворимости полимера принимается равным параметру растворимости жидкости, вызывающей максимальное набухание. Вещества близкого химического строения имеют близкие параметры растворимости и соответственно пониженную тенденцию к расслоению. К дискретной каучуковой фазе из двух сомономеров стирол имеет большее сродство [δ = 19,04 (МДж/м3)1/2], чем акрилонитрил [δ = 21,49(МДж/м3)1/2]. Поэтому концентрация стирола в дискретной фазе выше, чем в матрице. В результате такого распределения мономеров между фазами АБС-пластик обладает двумя особенностями:
1) цепи сополимера, привитые на эластомер, имеют большее содержание стирола по сравнению с непривитым матричным сополимером,
2) реакции линейной сополимеризации стирола с акрилонитрилом и гомополимеризации стирола протекают как в матричной, так и в дисперсной фазе (содержание окклюдированных полистирольных и линейных сополимерных частиц внутри каучуковой фазы достигает 60-90%).
Реакционная система в процессе полимеризации претерпевает инверсию фаз: при малых степенях конверсии мономеров дисперсной фазой служит каучуковая фаза, а при глубоких степенях (более 50%) конверсии каучуковые частицы становятся дискретными и диспергируют в непрерывной сополимерной матрице.
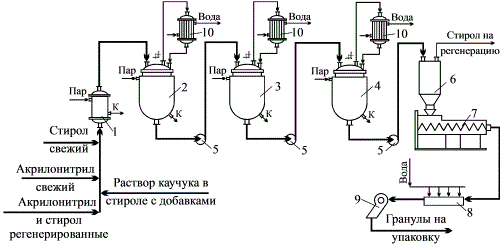
Смесь свежих и регенерированных мономеров (стирола и акрилонитрила), раствор синтетического каучука в стироле с добавками (инициатором, регулятором молекулярной массы, стабилизатором и пластификатором) с температурой 80-100 °С через кожухотрубчатый подогреватель 1 подают в первый корпус 2 комбинированного реактора непрерывного действия, снабженный быстроходной мешалкой (n = 0,5-1,5 об/с), обратным холодильником 10 и паровой рубашкой (реактор идеального смешения). При повышении по ходу реакционной системы температуры от 100 до 130 °С и времени пребывания в реакторе 5-6 ч степень конверсии мономеров достигает 30-45%. Реакционную массу первого корпуса по соединительному трубопроводу (реактору идеального вытеснения) насосом 5 подают во второй корпус 3 аналогичной конструкции, но снабженный тихоходной мешалкой (n = 0,03-0,13 об/с) в связи с высокой вязкостью поступающей исходной смеси. За 5-6 ч пребывания в корпусе 3 при температуре 130-160 °С степень конверсии мономера возрастает до 75-85%. В третьем корпусе 4 той же конструкции, что и корпус 3, при температуре 160-180 °С степень конверсии мономеров в процессах привитой и статистической сополимеризации повышают до 85-90%. В вакуумной камере при кратковременном пребывании полимеризата в зоне с температурой 200-240 °С отгоняют и направляют на регенерацию непрореагировавшие сомономеры, а общая степень конверсии достигает 90-95%. В экструдере 7 из расплава АБС-пластика формуют ленту (или пруток), которую охлаждают в ванне 8, измельчают на гранулы в дробилке 9 и направляют на упаковку.
Наряду с высокой эластичностью и ударной прочностью АБС-пластик характеризуется хорошей термостойкостью, способностью к металлизации, высокими диэлектрическими показателями, легкостью переработки в изделия всеми способами для термопластов (литьем под давлением, экструзией, вакуумформованием, каландрованием). Марочный состав его определяется назначением материала, включающим несколько групп: теплостойкие, ударопрочные, самозатухающие, наполненные стекловолокном и др.
АБС-пластик применяют в производстве труб для нефтепродуктов, при изготовлении гальванических ванн, металлизированных деталей автомобилей, корпусов приборов и отдельных деталей в электро- и радиотехнике, санитарно-технических изделий в строительстве.
Назад (ПМ на основе сополимеров стирола) Далее (Ударопрочный полистирол)