Сополимеры СФД и СТД
Целесообразность сополимеризации формальдегида с диоксоланом и триоксана с диоксоланом
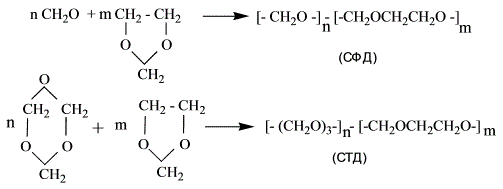
обусловлена возможностью повышения термостабильности полиформальдегида путем введения в полимерную цепь углерод-углеродных связей (С-С), тормозящих процесс деполимеризации (появление в макромолекуле фрагмента цепи, включающего два последовательно соединенных атома углерода, обрывает цепь деструкции полиформальдегида с отщеплением мономерного формальдегида). Изменением содержания звеньев сомономера диоксолана в сополимере можно в широких пределах варьировать свойства сополимера (обычно содержание звеньев диоксолана колеблется в пределах 2-6%). При этом доля неустойчивых концевых фрагментов макромолекул ~(OCH2)nОН обратно пропорциональна количеству введенного диоксолана, а доля термостабильного (до 270 °С) полимера составляет 85-95%. Стабилизированный сополимер в 3-4 раза более стабилен, чем ацетилированный гомополимер, легче перерабатывается в изделия, стоек к щелочам и растворам солей. Поэтому сополимеры вытесняют гомополимер.
Стабилизирующую добавку - сомономер диоксолан, представляющий собой жидкость с температурой кипения 75 °С, получают из этиленгликоля и формальдегида или триоксана:
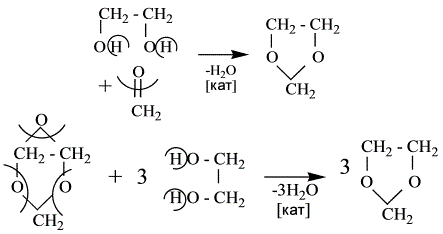
Процесс протекает при температуре 98-100 °С, в качестве катализаторов используют серную кислоту или другие соединения. Выделяющаяся при этом вода образует с диоксоланом азеотропную смесь, которую подвергают высаливанию 40%-ным раствором щелочи. Диоксолан-сырец очищают ректификацией до конечного содержания влаги в дистиллате 0,03%. Кроме диоксолана, в качестве стабилизирующей добавки в производстве СФД практическое промышленное применение получил также этиленоксид.
Производство сополимера формальдегида с 1,3-диоксоланом (СФД) включает ряд последовательно протекающих операций: 1 - загрузка в реактор-полимеризатор раствора диоксолана в циклогексане, 2 - загрузка при температуре 30-35 °С катализатора-эфирата трехфтористого бора [BF3-O(C4H9)2] и предварительно подвергнутого тонкой очистке формальдегида, 3 - установление температуры реакционной системы 35-45 °С и проведение полимеризации, 4 - разбавление реакционной массы сухим охлажденным циклогексаном и передавливание ее в отпарной аппарат, 5 - хвостовые операции, включающие разложение катализатора, разбавление суспензии водой, вакуумную фильтрацию ее, обработку полимера аммиачной водой (для связывания свободного формальдегида), отмывку и фильтрацию, сушку и грануляцию полимера.
Производство сополимера СТД предусматривает использование в качестве основного мономера триоксана - кристаллического вещества (Тпл=62 °С, Тк=114 °С), гидролизующегося в присутствии минеральных кислот до формальдегида и спонтанно полимеризующегося при плавлении и кристаллизации и содержании воды менее 1%.
Триоксан получают нагреванием концентрированного (60%) обезметаноленного раствора формальдегида до 100оС в присутствии кислого катализатора (H2SO4, катиониты). При температуре кипения смеси последовательно протекают реакции тримеризации и циклизации по схеме:
3CH2O + H2O --> HO-[-CH2O-]3-H <--> (-CH2O-)3 + H2O
Парообразные продукты реакции содержат до 14% триоксана, формальдегид и воду. Пары подвергают ректификации, дистиллат - экстракции бензолом, экстракт, содержащий 35% триоксана, - повторной ректификации.
Триоксан в отличие от формальдегида устойчив и легко очищается от полярных примесей (допустимое содержание в мономере метанола и воды 0,005 %, муравьиной кислоты 0,003 %). Триоксан легко и с хорошим качеством вступает в процессы гомополимеризации, но морфологические особенности получаемого при этом гомополимера не позволяют проводить гетерогенное ацетилирование. Поэтому необходима термостабилизация методом сополимеризации. Сополимеризация его с диксоланом протекает по катионному механизму в присутствии дибутилэфирата трехфтористого бора по уравнению

Процесс протекает в среде бензина под избыточным давлением 0,65-1 МПа. Экзотермика процесса сополимеризации в три с лишним раза меньше, чем при гомополимеризации ( Qгомо-экзо = 71 кДж/моль, Qсопол-экзо = 22,6 кДж/моль).
Сополимеризацию можно проводить в растворе и в расплаве.
Растворный способ проведения процесса включает два варианта: 1) в неполярном растворителе - бензине; 2) в присутствии небольших количеств высокополярного инертного вещества (полярной добавки), растворенного в триоксане и не смешивающегося с неполярным растворителем (бензином). Расплавный способ реализуют организацией процесса в тонком слое расплава триоксана с диоксоланом при интенсивном перемешивании (гарантирует полный отвод экзотермики) в двухшнековом реакторе - экструдере в течение нескольких минут.
Растворный способ проведения сополимеризации не требует применения специального технологического оборудования. Обычно процесс проводят путем растворения сомономеров в бензине при концентрации по триоксану 40-50% и диоксолану 1,5-2% в течение нескольких часов до достижения степени конверсии 35-60%.
При сополимеризации с применением высокополярной добавки, например, пропиленкарбоната
(Тк = 241,7 С),
степень конверсии сомономеров повышается до 95-98%, увеличивается молекулярная масса и термостабильность полимера. Полимеризация начинается в гомогенных условиях при высокой концентрации триоксана. По мере расходования триоксана нарушается термодинамическое равновесие процесса сополимеризации и происходит фазообразование. При этом образуются две жидкие фазы: а) неполярная фаза, включающая бензин и триоксан (дисперсионная среда), б) полярная фаза, содержащая в основном полярную добавку и сомономеры (дисперсная фаза), выделяющаяся на поверхности твердого полимера. Вследствие фазообразования наблюдается значительное ускорение процесса полимеризации, что объясняется высокой (на уровне 50-80%) и постоянной вплоть до 98%-ной степени конверсии концентрации мономеров в полярной фазе. Этому способствует небольшой объем полярной фазы (меньше 5-10% объема полимеризата) и возможность восполнения мономеров путем диффузии из дисперсионной фазы.
Назад (Производство гомополиформальдегида) Далее (Производство СТД)